IoT·ICT 결합시켜 경쟁력 높이고
불량률 90% 줄여 연간 1억 절감
차량 판매 후 불량 확인도 쉬워져
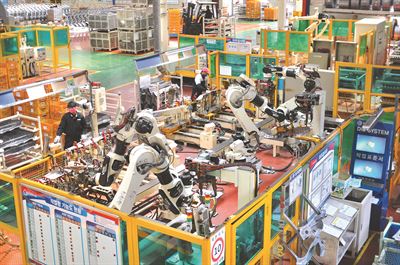
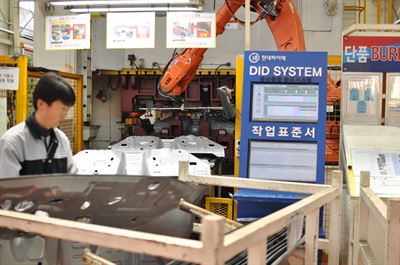
정부가 제조업의 혁신을 표방하며 강조한 것이 바로 스마트 공장이다. 스마트 공장이란 사물인터넷(IoT) 등 정보통신기술(ICT)을 접목해 공장 시설과 운영을 최첨단으로 자동화하는 것이다. 이를 통해 사람이 하다 보면 발생할 수 있는 오류를 줄이고, 자동으로 수리 및 교체시기를 파악해 사고나 불량을 방지한다. 그만큼 기업의 경쟁력을 높일 수 있어 전세계 기업들이 앞다퉈 스마트 공장을 추진하고 있다.
지난 26일 방문한 광주 하남산업단지 내 현대하이텍 공장은 국내의 대표적 스마트 공장이다. 현대ㆍ기아자동차의 1차 협력업체로 자동차용 강판 생산 및 조립을 담당하는 현대하이텍은 지난해 스마트 공장을 만들어 연간 용접 불량을 90% 줄였고 프레스로 찍어낸 강판 불량도 80% 감소시켰다. 절감 비용은 연간 1억원 이상이다. 현대하이텍 관계자는 “지난해 15억원을 들여 스마트 공장용 시스템을 갖췄다”며 “불량률 감소로 제품 신뢰도가 올라간 것이 가장 큰 성과”라고 말했다.
현대하이텍 공장은 쏘울 및 뉴 카렌스의 엔진룸과 차량 실내 사이에 들어가는 격벽, 뒤쪽 휠베이스에서 창문으로 이어지는 철제 구조물, 문 안쪽의 강판 등을 매일 1,000대분 이상 생산한다. 주로 금형 위에 놓고 찍어낸 강판을 용접해 구조물을 만든다.
낮 12시 10분, 작업 시작을 알리는 벨이 울리자 400~1,200톤에 압력을 가하는 프레스 기계가 굉음을 내며 철판을 찍어내기 시작했다. 스마트 공장으로 변신한 이후 프레스 기계 옆 모니터에 지금까지 찍어낸 수량과 몇 개를 찍으면 날이 무뎌진 금형을 수리해야 하는지, 금형에 묻은 이물질을 닦아줘야 하는지 표시됐다. 금형을 수리할 시기가 되면 자동 경보도 울린다.
스마트 공장이 되기 전에는 일일이 손으로 기록하며 관리해 수리나 세척, 교체 시기를 넘기는 일이 잦았다. 그만큼 불량품이 나올 수밖에 없었다.
이렇게 찍어낸 철판은 다른 철판과 용접해 하나의 구조물이 된다. 용접 공정에 셀 수 없이 많은 감지기(센서)들이 달라붙어 전압과 용접 상태를 실시간 감시한다. 이것도 모니터 화면에 표시되는데 용접이 잘 되지 않은 부분은 붉은색으로 표시돼 문제 발생 부분을 바로 알 수 있다..
공장 한쪽의 ‘전파괴검사실’에서는 용접이 잘 됐는지 재차 확인한다. 아스팔트에 구멍을 뚫는 전동드릴로 접합 부위를 뜯어내는데, 용접 부위가 다른 쪽 철판에 붙어 구멍이 나면서 분리돼야 정상이다. 임완섭 현대하이텍 전무는 “살점이 뜯겨 나와야 양산품”이라고 설명했다.
현대하이텍은 제품 추적관리시스템까지 갖춰 올해 안에 스마트 공장을 완성할 계획이다. 차량 판매 후에도 불량이 발견되면 쉽게 확인하기 위해서다. 이를 위해 광주의 창조경제혁신센터도 올해부터 현대하이텍을 비롯한 40개사에 2,000만원씩 지원한다. 임 전무는 “스마트 공장으로 변신한 뒤 철판 사출 및 용접 상태를 보면 세계 3위 안에 든다”며 “비싼 수입차 못지 않다”고 강조했다.
광주=글ㆍ사진 허정헌기자 xscope@hk.co.kr
기사 URL이 복사되었습니다.
댓글0