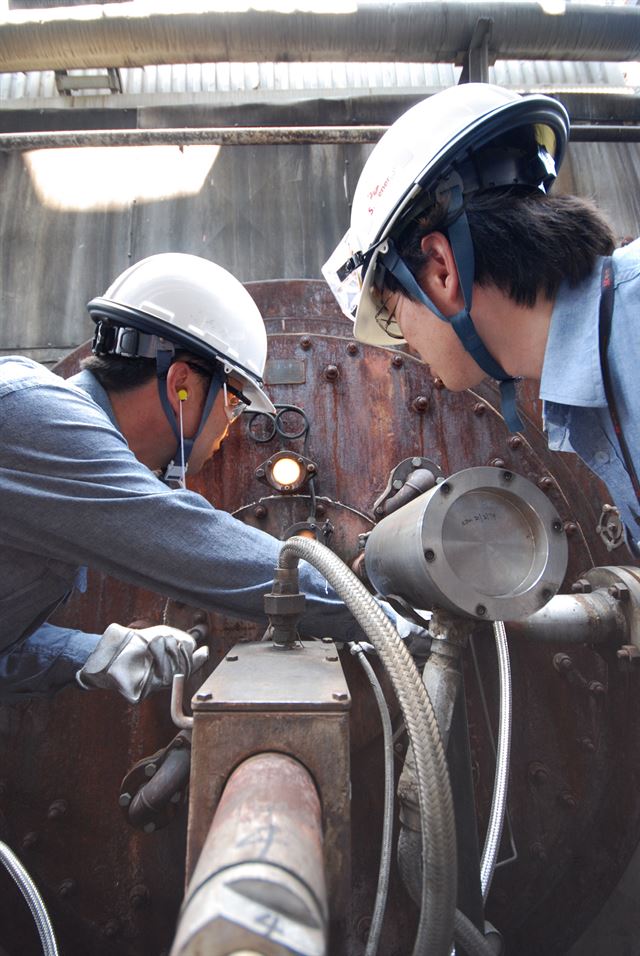
지난달 16일 포스코가 자체 ‘안전점검의 날’을 맞아 포항ㆍ광양 제철소 내 각 공장에서 실시한 안전점검은 매년 진행하던 방식과는 조금 다르게 이뤄졌다. 누수, 균열 등 이미 진행된 사고 징후들을 찾던 것에서, 특별한 조짐이 없지만 현장 상황과 작업자의 부주의에 따라 사고가 날 수 있는 요소를 찾아 미리 대응하는 데 초점을 맞춘 것. 실제 이날 안전팀 직원들은 ▦가동 중인 설비 ▦추락 ▦낙하물 ▦가스중독 및 질식 ▦크레인 등 5대 위험요인을 선정해 각 항목별 위험요소에 대한 점검을 벌였다.
이는 지난 달 초 영국 런던에서 열린 세계철강협회(WSA) 정기이사회 결의에 따른 것. WSA는 50여개 회원사들에게 4월 중 하루를 안전점검의 날로 지정해 자체 점검을 실시, 각 위험요소를 보고하라고 당부했다. 회사 관계자는 “무심코 넘길 수 있었던 작은 부분들을 다시 한번 살펴 보게 된 좋은 기회였다”라고 말했다.
안전경영에 대한 중요성이 커질수록 기업들은 현장으로 눈을 돌리고 있다. 작업 현장과 무관한 추상적이고 일반적인 수준의 안전수칙만으론 다양한 위험요소와 그에 따른 사고에 효율적으로 대응하기 힘들기 때문. 따라서 기업들은 각각의 현장을 정확히 파악해 이를 반영한 가이드라인을 만들고 있다.
포스코가 자체 개발한 안전 진단 및 컨설팅 시스템인 ‘PSRS(POSCO Rating System)’가 대표적인 사례. 지난 2009년 도입된 PSRS는 현장 직원 인터뷰, 설문 분석 등을 통해 작업장 내 위험요소를 찾고 그 결과를 정량적 수치로 환산한 뒤, 개선방향을 제시한다. 특히 진단과정에선 시설 등 작업환경은 물론, 사고 발생 시 즉각적인 대응을 위한 보고 체계 등 시스템 측면까지 다룬다. 이를 바탕으로 만들어진 상황별 매뉴얼은 100여 가지에 달한다.
안전점검 활동 주체 역시 현장 전문가들이다. 현재 산업안전기사 1급 이상 전문인력 30여명이 포항과 광양에 상주하고 있고, 자체 선발한 ‘안전 마스터’가 제철소 내 소단위 공장마다 1, 2명씩 배치돼 매일 설비와 안전장치를 점검하고 있다.
SK이노베이션은 울산, 인천, 증평, 청주, 서산, 대전 등 국내를 포함해 해외 모든 생산 현장 별 안전관리 세부지침인 ‘세이프티 골든 룰’을 마련하고 있다. 사업장마다 생산 품목이나 환경이 다른 만큼, 사고위험이 높다고 생각되는 항목을 10개씩 정하고 이에 대한 행동수칙을 정리한 것이다.
예를 들어 밀폐공간이 많은 울산 공장 내 생산시설에선 정해진 주기마다 유해공기의 농도를 측정하도록 하고, 다양한 화학실험이 이뤄지는 대전연구원에선 취급하는 화학물질에 대해 각각의 특성이 기재된 명세서인 ‘MSDS(물질보건안전자료)’를 반드시 숙지하도록 하는 식이다. 평상 시 지침에 따른 예방활동이 이뤄지며, 사고 시에도 이 지침에 대한 위반여부를 중점적으로 조사해 책임을 묻는다.
강화되는 화학물질 관리제도 역시, 현장 근로자를 중심에 놓고 만들고 있다. 최근 도입한 ‘화학물질 위험성평가 체계’의 경우, 근로자가 작업방법 및 시설 개선사항을 건의하면 이를 적극 반영해 지속적으로 기준을 보완해 나간다. 이밖에 최고경영자 직속 안전ㆍ환경 전담조직이자 모든 안전 관련 사안을 실행하는 독립부서인 ‘SHE(SafetyㆍHealthㆍEnvironment)’가 제 역할을 하는지 살피는 감사 권한 역시 각 생산팀 내 전담직원에게 맡기는 파격적인 실험도 하고 있다. 회사 관계자는 “현장 근로자들의 다양한 목소리를 충분히 반영해 관련 규정을 만들고 있다”며 “좀 더 안전한 일터를 만들기 위해 참여 폭을 더욱 늘려 나갈 계획”이라고 말했다.
김현수기자 ddackue@hk.co.kr
기사 URL이 복사되었습니다.
댓글0