'머리카락 20분의 1' 두께 동박 30㎞ 뽑아내
찢어지거나 주름 안 생기도록…"기술력 덕분"
국내서만 연간 전기차 130만 대 분량 동박 생산
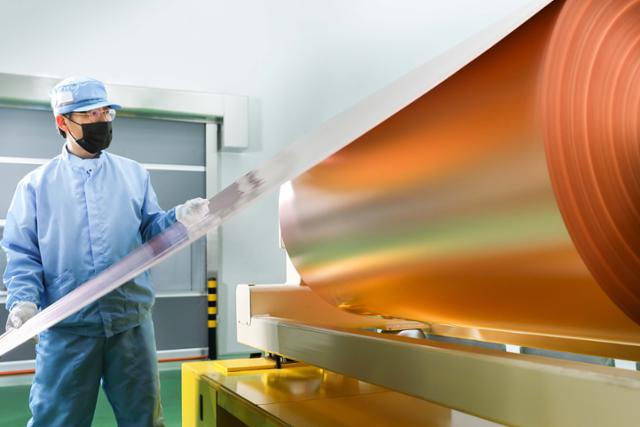
전북 정읍시 SK넥실리스 동박 공장에서 한 직원이 동박 롤에 이상이 없는지 확인하고 있다. SKC 제공
#. 머리카락처럼 생긴 불그스름한 선들이 커다란 포대에 담겨 있다. 다 쓴 전선에서 뽑아낸 얇고 긴 구리 스크랩이다. 바닥에는 지름이 3m쯤 되는 납작한 원통형 수조(용해조)가 여럿 있다. 구리 스크랩을 이 수조 안에 옮겨 담으면 폐전선이 변신을 시작한다. "수조에는 황산액이 들어 있어요. 이 액체는 본래 맑은데 구리를 담그면 '황산구리 도금액'으로 바뀌면서 색도 파랗게 됩니다." 임기영 SK넥실리스 동박생산팀장이 동박을 만드는 첫 단계를 설명했다.
지난달 18일 찾은 전북 정읍시 SK넥실리스 제3공장에선 원재료 구리를 녹여 도금액을 만드는 공정(용해공정)이 한창이었다. 동박은 구리를 고도의 공정 기술로 얇게 만든 막이다. 이차전지(배터리) 속 음극의 집전체 역할을 하는 핵심 소재다. 전기차 한 대에 40㎏ 정도 들어간다. 공장에 들어오기 전 동박 전시실에서 본 얇은 금빛 포일은 폭이 넓은 두루마리 형태로 말려 있었는데 원재료를 보니 그 생산 과정이 얼른 그려지지 않았다.
공장 내부는 모든 것이 멈춘 듯 정적뿐이었다. 사람의 역할이 적고 대부분 공정이 수조 아래에서 이뤄지기 때문이다. 용해조 아래에서는 도금액이 여러 탱크를 돌아다니며 24시간, 365일 구리를 녹여내고 있다고 한다. 하루에 100~150톤(t)의 폐전선이 재료로 쓰인다. 김동우 SK넥실리스 동박공정기술개발팀장은 "메인 탱크에서 배관을 통해 돌고 있는 도금액이 각 탱크 아래에 있는데 원재료인 구리를 여기에 넣는다"며 "도금액을 한번 만들면 버리지 않고 계속 쓰기 때문에 이 용액에 불순물 없는 상태로 유지하는 게 중요하다"고 설명했다.
동박을 만드는 원리는 간단하다. 전해액 수조 양끝에 양극과 음극을 설치한 뒤 전기를 흘려주면 이온이 이동한다. 음극에 달라붙은 구리는 물레방아처럼 도는 드럼 모양의 제박기에 붙어 올라온다. 김 팀장은 "드럼의 반원 아래쪽 절반은 도금액에 담겨 있는데 거기서 도금 공정이 이뤄진다"며 "구리가 회전하는 드럼 겉면에 붙으면 한 바퀴 도는 사이 공기에 노출되면서 박리된다"고 설명했다.
세계 1위 동박 기술? "얼마나 얇게 박리시키는가" 관건
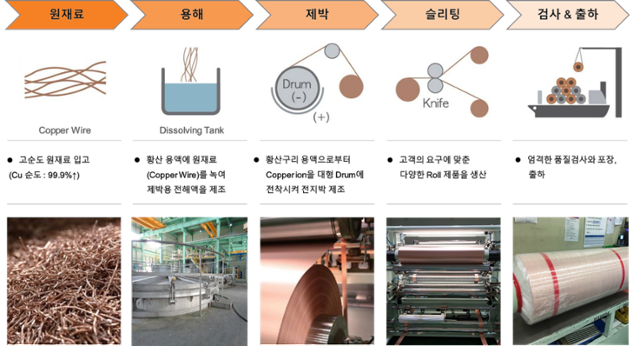
동박 생산 공정. SK넥실리스 제공
세계 1위 동박 기술의 '레시피'는 여기 숨어 있다. 이차전지용 동박 롤 제품은 수십 ㎞에 이른다. 마이크로미터(㎛) 단위의 얇은 동박을 찢어지지 않게 만드는 데 노하우가 필요하다. 김 팀장은 "머리카락의 20분의 1 두께인 동박을 넓게 뽑아내려면 찢어지거나 주름이 생기기 쉬운데 그걸 없애는 게 기술력"이라며 "제박기는 사흘을 돌려야 하는데 이걸 펼치면 서울~천안 거리"라고 설명했다. SK넥실리스는 2021년 세계에서 가장 얇은 4㎛ 두께의 전지박을 1.4m의 광폭으로 총 30㎞ 길이로 뽑아내는 데 성공했다. 세계 최초다.
앞서 회사는 이런 기술로 2013년 세계에서 처음으로 6㎛ 두께 동박 양산에 성공했다. 2017년엔 최초로 5㎛ 동박을 제작했다. 지난해에는 세계 최초로 초고강도 동박(U 동박)과 원통형 배터리용 고연신(高延伸) 동박(V동박)을 개발했다.
연결된 통로를 따라 세계 동박 공장 중 높은 생산성을 자랑하는 4공장으로 향했다. 4~6공장은 최신 설비를 갖춘 신공장이다. 제박기 한 대당 생산량은 3공장 대비 30~40% 더 높다고 한다. 대부분 공정이 디지털 컨트롤 시스템(DCS)으로 이뤄진다. 질서 정연하게 놓인 제박기에 동박이 다 감기면 그때 비로소 직원이 범퍼카처럼 생긴 노란 차량으로 옮길 뿐이다.
200m쯤 떨어진 옆 방에는 형광등 빛을 받아 반짝이는 동박 두루마리가 9행 5열로 가지런히 줄 서 있었다. 이렇게 하루 동안 '숙성의 시간'을 보낸다. 서동석 SK넥실리스 ER지원팀장은 "물성(物性)이 퍼져서 균일해지는 데 하루 정도 걸려서 숙성 뒤 자른다"고 설명했다.
고객의 요구에 맞는 크기로 동박을 자르는 슬리팅 공정은 세차장 입구처럼 발이 드리운 구조물 안에서 이뤄졌다. 넓은 폭으로 만든 제품을 자르는 공간이다. 하늘색 옷과 모자를 쓴 직원 세 명이 세차기 모양의 설비 앞에 서서 컴퓨터를 들여다보며 어떤 제품을 자를지 결정하거나 꼼꼼히 제품 정보를 입력하고 있었다. 다른 한 사람은 동박을 잘라낸 뒤 구겨진 부분을 잘라내 버리면서 제품의 순도를 높이고 있었다.
11만5,700㎡(약 3만5,000평) 규모인 이 공장에서 생산하는 동박은 연간 5만3,000톤(t). 전기차 130만 대에 들어가는 배터리를 만들 수 있는 규모다. 다음 달 상업 생산을 앞둔 말레이시아 공장과 지난해 공사를 시작한 폴란드 공장도 비슷한 크기다. 세 공장이 모두 가동되면 이 회사는 총 15만여 t의 동박을 생산할 전망이다.
기사 URL이 복사되었습니다.
댓글0